A while back I was working entertainment tech for a small convention, I was the Sound Designer and had inherited the Power Design (usually done by the Lighting department, but we did not find a Lighting Designer until very late). The event was held at a hotel with a 4-section ballroom, call the sections 1, 2, 3, and 4. The stage was set in section 4 and we had a social event in sections 1 and 2 on Friday night with the airwall between 2 and 3 in place. After the social event the airwall between 2 and 3 was struck and the airwall between 1 and 2 was installed. For the remainder of the weekend events were on the stage in section 4 with audience in sections 2 and 3 and section 1 was the performer Green Room.
Power
We were told that we had one 100A 3-phase feed to use (as per the contract with the hotel). We were also told that there were feeders in the airwall pockets between sections 1 and 2 and sections 3 and 4. Call the pocket between 1 and 2 feeder A and the feeder between 3 and 4 we’ll call C and we’ll leave the label feeder B for the airwall pocket between sections 2 and 3 (which we were told did not have a feeder). We decided to use feeder C (airwall pocket between section 3 and 4, nearest to the stage).
100A of 3-phase 120v/208v power gives us 300A of single phase 120v power, but for safety I derated to 80% or 240A. I built the power budget and came out to just about 230A. I assembled my equipment (PDUs) and cable (cam-lock feeders, as well as NEMA 5-15 extension cords) to handle all our needs assuming we were getting all our power from feeder C near the stage.
Contact with the Enemy
When we arrived on Friday morning we discovered that feeder A and C were not 100A, but only 80A. Feeder B was 100A, but if we used it, then we would end up with a PDU in a bad location due to cable lengths. Feeder A and C both came from a power panel in the kitchen behind the ballroom. Feeder B came from a different panel further back in the kitchen, and that panel also fed the panel that fed A and C. Like this:
Panel 1 -> Feeder B (100A)
Panel 1 -> Panel 2 -> Feeder A and C (80A)
We contacted Hotel Engineering and they apologized for getting us bad information. They offered to let us use as many of the different power feeds that we needed to, at no extra cost, to get the job done.
We were not comfortable using just the 80A feeder C as we were very close to that total draw and rather than use feeder B and have a PDU badly located, and against my better judgement, we decided to split the power between feeder C (for the stage) and feeder B (sound and lighting control points and video production control all at the back of the room). We knew where each feeder came from, we knew how the panels tied together, what could go wrong?
Friday night, after the social event, we started setting up the sound and lighting control riser; the video crew started building video production control on the other side of the room. I was the first to tie the two power feeds together when I plugged the mixer outputs into the snake feeding the FOH amp rack. As soon as the connectors mated I heard a hum out of the mains. I immediately knew what was going on. I called the crew together and told them we had a serious potential difference between safety grounds between feeder B and C. One of the crew grabbed a 100′ 12/3 extension cord and ran it diagonally across the room from feeder C to the sound board. We measured over 100mV between the safety ground pins. We assumed there was a wiring fault somewhere between the panels and feeders.
So what do we do now? The first thought was to use a bonding conductor to tie the two safety grounds together. We tried connecting the ground pin of that extension cord to the ground pin of the power from feeder B. That reduced the hum by about 20 dB, but it was still clearly audible. It was clear that we could not get a low enough impedance connection with the 12 AWG power cords we had with us.
We ended up, at midnight, redesigning the power distribution based on the parts we had on hand. We used feeder B since it could carry our full load. One of the PDUs that we added to the order at the last minute combined with multiple sets of camlock T’s of various genders, enabled us to get power where we needed it, but it was not pretty.
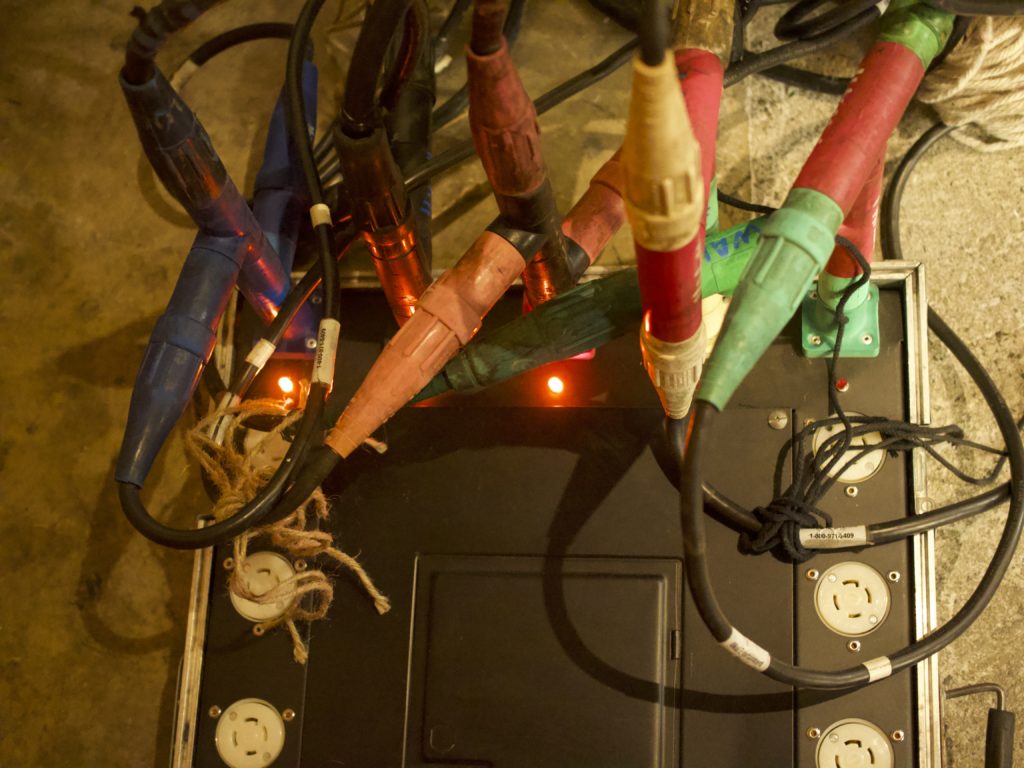